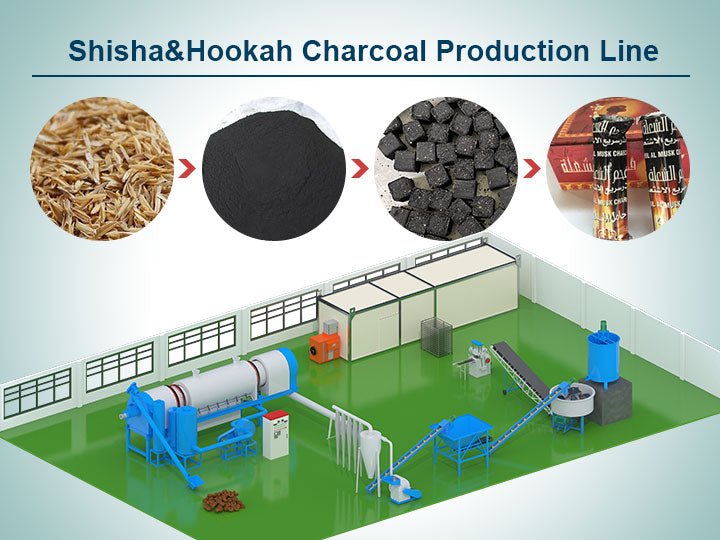
How Shisha Charcoal is Made: A Detailed Guide
Share
Shisha smoking is a popular pastime enjoyed by many around the world. Central to this experience is the charcoal used to heat the shisha tobacco, which significantly affects the flavor and quality of the smoke. Understanding how shisha charcoal is made can help you appreciate the craftsmanship behind each piece and choose the best option for your sessions. This comprehensive guide delves into the intricate process of making shisha charcoal, from raw materials to the final product.
Table of Contents
- Introduction
- Types of Shisha Charcoal
- Raw Materials
- The Manufacturing Process
- Carbonization
- Crushing and Mixing
- Shaping and Molding
- Drying and Curing
- Quality Control
- Environmental Considerations
- Conclusion
1. Introduction
Shisha charcoal, often made from natural materials like coconut shells or hardwood, plays a crucial role in the shisha smoking experience. It provides the necessary heat to vaporize the shisha tobacco, allowing for a smooth and flavorful smoke. The process of making shisha charcoal is meticulous and involves several stages to ensure high quality and performance.
2. Types of Shisha Charcoal
There are primarily two types of shisha charcoal:
Natural Charcoal
Natural charcoal is made from organic materials such as coconut shells, bamboo, or hardwood. It is chemical-free, burns longer, and provides consistent heat, enhancing the flavor of the shisha tobacco. Popular brands include CocoNara and Fumari.
Quick-Light Charcoal
Quick-light charcoal contains chemical additives that allow it to ignite quickly with a lighter or match. It is convenient for on-the-go use but may impart a chemical taste to the shisha. Brands like Three Kings are well-known in this category.
3. Raw Materials
The quality of shisha charcoal depends heavily on the raw materials used. Common materials include:
- Coconut Shells: Renowned for their high heat output and long burn time, making them a preferred choice for many shisha enthusiasts.
- Hardwood: Provides a robust and consistent heat source, often used in natural charcoal varieties.
- Bamboo: Another sustainable option, known for its clean burn and minimal ash production.

4. The Manufacturing Process
The process of making shisha charcoal involves several critical steps to ensure the final product is of high quality.
Carbonization
The first step is carbonization, where the raw materials are burned in a controlled environment with limited oxygen. This process converts the organic material into charcoal by removing moisture and volatile compounds.
- Kilns or Retorts: The materials are placed in large kilns or retorts and heated to temperatures between 400-700°C (752-1292°F). The absence of oxygen prevents the materials from burning completely and allows them to carbonize.
Crushing and Mixing
Once carbonized, the charcoal is crushed into a fine powder. This powder is then mixed with a natural binder, such as cornstarch or tapioca, to help the charcoal pieces hold their shape.
- Mixers: Industrial mixers ensure the charcoal powder and binder are thoroughly combined, resulting in a uniform mixture.
Shaping and Molding
The charcoal mixture is then shaped into briquettes, cubes, or other forms using molds.
- Molding Machines: These machines compress the mixture into the desired shapes under high pressure, ensuring each piece is dense and consistent.

Drying and Curing
The shaped charcoal pieces are dried to remove any remaining moisture. This step is crucial for ensuring the charcoal lights easily and burns evenly.
- Drying Chambers: The charcoal is placed in drying chambers with controlled temperatures and airflow to ensure thorough drying.
- Curing: Some charcoals are cured for an extended period to enhance their hardness and burn quality.
5. Quality Control
Quality control is a vital part of the manufacturing process. Each batch of charcoal undergoes rigorous testing to ensure it meets industry standards for burn time, heat output, and ash production.
- Burn Tests: Samples are lit and monitored to check for even burning and heat consistency.
- Ash Content: The amount of ash produced is measured to ensure it falls within acceptable limits.
6. Environmental Considerations
Many manufacturers are adopting environmentally friendly practices to reduce their carbon footprint. This includes using sustainable raw materials, optimizing the carbonization process to reduce emissions, and implementing waste management systems.
- Sustainability: Using coconut shells and bamboo, which are renewable resources, helps minimize environmental impact.
- Waste Management: Efficient waste management practices ensure minimal environmental pollution from production processes.
7. Conclusion
The process of making shisha charcoal is intricate and requires careful attention to detail to produce high-quality products. From selecting the right raw materials to ensuring rigorous quality control, each step is crucial for delivering a superior shisha experience. Understanding how shisha charcoal is made can help you make informed choices and appreciate the craftsmanship behind each piece.
For more tips and information about shisha, visit LocosShisha.com. Enjoy your shisha sessions and smoke responsibly!